Case Study: Asset Tracking Solution for Hospitals
FCL Components IoT Devices Set UMC Utrecht On Path to Precise Asset Tracking
In hospitals of all sizes, medical devices are frequently moved from one room to another or from one department to another. For nurses and other employees—especially those who work in larger facilities—locating and tracking these devices often involves time and energy. University Medical Centre Utrecht (UMC) in Utrecht, The Netherlands, whose more than 1,100 beds and 11,000-plus employees rank it among the nation’s largest healthcare facilities, is successfully addressing these issues using an asset tracking solution that leverages anchors, tags, and USB dongles from FCL Components, with mesh network connectivity afforded by FCL Components partner Wirepas.
The cost-effective, easy-to-install solution allows hospital staff to quickly determine the whereabouts of medical devices at all times and, in turn, better focus on their primary task of providing quality patient care. It is readily extendible from one floor to a full building and from a single building to an entire campus, with no limit to the number of devices being tracked. The very light mesh network infrastructure used for asset tracking can potentially be used for other purposes throughout the hospital, such as indoor wayfinding; sensor monitoring of room temperatures, humidity, CO2, and/or sound levels, and lighting control.
Big Challenges, Big Goals
Enabling staff to locate medical devices anywhere within the hospital had long been an objective at the UMC Utrecht. However, several obstacles and goals that surfaced over the past few years made it even more important for the hospital to find an asset management solution.Pressure to increase both overall organizational and device usage efficiencies and agility while conserving costs—a pervasive concern in the medical sector as a whole—topped the list of challenges. So, too, did the amount of valuable time spent by healthcare staff to locate the necessary medical equipment for each case. The more time employees devoted to finding this equipment, the less effort they could devote to focusing on and providing quality patient care.
Meanwhile, ensuring that medical devices would always be safely deployable was a top priority. Not only did hospital staff need a way to find these devices; they also required a means of reviewing each device’s “history” to confirm whether and when it had been cleaned, undergone preventive maintenance, and the like.
In Search of Accuracy, Scalability—and More
The UMC Utrecht took a multidisciplinary approach to identifying a solution that would best help to address its challenges and achieve its goals. Workgroups from a variety of disciplines, including IT, medical technology, care, and facilities, collaborated toward this end.In general, the UMC Utrecht wanted to build a reliable asset tracking solution that could be deployed without investing money and time in cabling. In addition to an IoT backbone, the solution had to afford centralized vision and ownership of hospital assets and asset maintenance tasks, overseen by an internal “medical device service.” It also needed to:
- Be highly appropriate for use in a hospital application
- Offer a high degree of localization accuracy
- Carry a reasonable cost for system installation and per tracked item
- Be scalable to accommodate increases in surface coverage and number of assets tracked
- Be future proof, with an ample degree of openness, extensibility, and flexibility to handle evolving usage requirements and needs
- Support the tracking of many kinds of devices, from large pieces of equipment used at patients' bedside to smaller items, such as thermometers
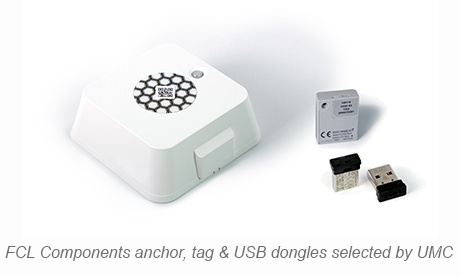
Solution Combines FCL Components Hardware With Wirepas Mesh Connectivity
The UMC Utrecht took a multidisciplinary approach to identifying a solution that would best help to address its challenges and achieve its goals. Workgroups from a variety of disciplines, including IT, medical technology, care, and facilities, collaborated toward this end.After extensive consideration, the team opted for a solution comprised of FCL Components USB dongles, Z08 anchors with Wirepas mesh network connectivity, and FWM8BLZ08T tags. The anchors and tags are small radio emitters that function in a manner similar to Bluetooth Low Energy (BLE). Tags are attached to each asset tracked, while a network of anchors is installed at fixed positions throughout the hospital building. The anchors function as position reference points and emit signals to the tags, with the level of signal received by a given tag used to calculate its position (and hence, the location of the asset). Location information is sent from the anchors to a central point (gateway) that transfers the data to a server. The solution also features a dashboard that provides an overview of data collected through the sensors. Built on Columna Flow software from Systematic, the dashboard gives hospital staff a means of searching for a specific medical device or, with more search options, for a category of devices. Users get a quick overview of relevant medical devices, clearly marked based on availability and status (such as sanitation status).
The UMC Utrecht selected the solution and its components based on their close match with the evaluation criteria and the advantages they were found to provide, including the ability to add more hardware later and to resist interference. Specifically, the FCL Components Z08 anchors won favor because they operate on four AA batteries with a lifetime of 10 years, limiting maintenance requirements. The hardware was also chosen because its design could be optimized for installation in a hospital setting.
Meanwhile, the FCL Components USB Wirepas dongles, which are used as routers/nodes to extend the mesh network, got the green light in large part because they can be mounted on Wi-Fi access points. Instead of working on batteries, the dongles derive power from the access points, eliminating the need for extra power cables and batteries and enabling obstacle-free increases to network coverage.
Additional, over-arching benefits afforded by the solution include:
Cost and time savings
Anchors and tags are inexpensive and run-on low energy or are battery-operated, with no costly cabling or antennas needed. The devices are delivered preconfigured, simplifying installation, and further keeping implementation expenditures in check. Unlike asset tracking systems that use BLE or Wi-Fi technology, the solution allows for coverage of an entire hospital floor with one GW of power—no struggling with cabling to source power or connect to the internet. The addition of battery-operated router nodes facilitates easy expansion of the network at a significantly lower cost than for other types of systems; the larger the facility, the greater the savings.Suitability for hospital use
The solution’s radio frequency and power do not interfere with UMC’s Wi-Fi or with the operation of any medical equipment. Additionally, the design of the anchors is optimized for deployment in a hospital application: they are water-resistant (IP65-rated), easy to clean, and were adapted to feature appropriately colored (white) enclosures and a non-angular shape. Anchor operation via four AA batteries or USB power yields long-lasting energy and minimizes maintenance needs.Scalability
The Wirepas mesh network can be expanded with no limits; increasing the coverage area requires only the addition of more anchors. Preconfigured anchors (delivered by FCL Components) can be automatically integrated into the network when switched on in the hospital. Extra tags can also be added to effortlessly increase the number of devices tracked by the system.Future-proof
Besides asset tracking, the mesh network can be harnessed for sensor monitoring (temperature, CO2 levels, and the like) as well as in wayfinding systems inside the hospital. Sensors and tags from other manufacturers in the Wirepas ecosystem can be added if needed.Reliability and accuracy
The Wirepas mesh network is self-healing; if one communication node is removed, another node is automatically selected. No external intervention is needed to repair the network. The solution features a tag position accuracy of approximately 16 feet, sufficient to meet the hospital’s needs.
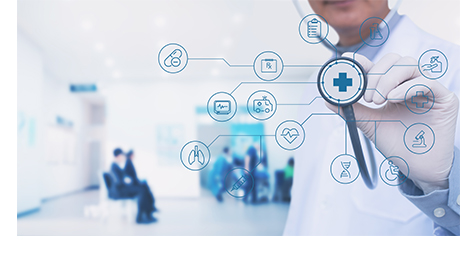
Results: Right Equipment, Right Time, Right Patient Care
Following a pilot implementation, the asset tracking solution is currently being rolled out. All deployment is occurring with minimal interruption to healthcare service delivery.According to hospital officials, the solution frees up hospital staff to pay attention to their core tasks; healthcare workers no longer waste valuable time locating the right equipment and ensuring that it is ready for use. This improves the caliber of care afforded to all patients. Facilities managers can easily see where “clusters” of equipment are located and move it elsewhere in the hospital to meet specific needs.
Additionally, the UMC Utrecht can now set minimum and maximum equipment stock levels, limiting unnecessary equipment expenditures while ensuring that sufficient quantities of the right devices are on hand where and when they are needed. The end-result is not only financial savings, but once again, higher-quality patient care.
UMC Utrecht’s future plans for the solution will likely involve leveraging it in applications other than tracking medical devices—an option deemed desirable by the multidisciplinary team at the outset of the project. The solution architecture is extendible to the monitoring of environmental conditions within the hospital facility, such as temperature, humidity, air pressure, luminance, and sound levels, as well as of processing flows.
With FCL Components hardware as a backbone, UMC Utrecht clearly has the power to better track its assets—and avail itself of enhanced tracking and monitoring capabilities beyond the realm of devices—now and in the future.