Product Highlights: FBR53-HC Relay
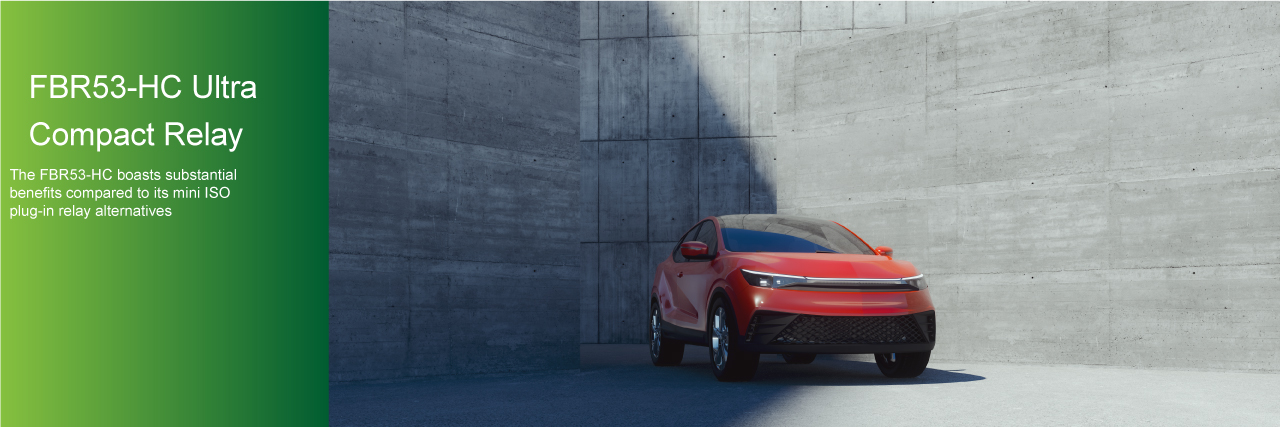
FCL Components' FBR53-HC ultra compact 50A PCB/THR Relay Ready to replace Mini ISO!
FCL Components recently introduced a brand-new miniature PCB-relay: the FBR53-HC, 50A/14VDC/12V coil for medium-to-heavy Automotive loads. Despite its modest appearance, it boasts substantial benefits compared to its Mini ISO plug-in relay alternatives. Not only is it much smaller, thanks to its twin contact design it also generates less heat and consumes a lot less power.
Even though car sales figures are lagging because of the obvious corona precautions restricting travels, the development of new mobility solutions is steadily on the move. One of the undeniable trends is electrification, and with it the need for more reliable and durable power management systems and direct current switches that meet today’s challenging requirements. With this in mind, FCL Components Ltd. developed a new relay: the FBR53-HC. It is developed around three core principles, solving four crucial customer requirements with five key technologies.
Three core principles
With many decades of experience when it comes to relay manufacturing, FCL Components has over the years distinguished three core principles that always take center stage when developing a new one. First of all, each FCL Components' relay is as reliable as possible. A relay can be packed with the greatest features in the world, but is costly when it does not work, and so reliability always comes first. The second core principle is reducing size and light weight. Especially in automotive applications, space comes at a premium. So contrary to some beliefs, smaller is usually better. Which brings us to the third core principle: design. To get great value out of a small relay, one needs clever and robust design strategies in place that address both electrical and mechanical challenges. The design should not only consider operational requirements but should also include the manufacturing process. In the case of the new FBR53-HC, this holistic approach has resulted in a significantly smaller size (up to 80% in volume) when compared to Mini ISO types, a much better performance (less heat dissipation and power consumption), even in harsh conditions (-40 to +125°C ), and a significantly longer lifetime compared to your typical plug-in relay.
Achieving four goals...
Where do automotive customers score highly when adding value? FCL Components found four big cost savers when it comes to selecting the right relay for the job. First comes reducing failure. This is obvious with regard to avoiding failures during operations, but also holds true for 0 km failure, reducing rejects during manufacturing. But there are other factors that substantially lower manufacturing costs and increase the durability, and thus lifespan, of a relay. Examples include using reflow soldering techniques and improving mechanical and electrical performance. FCL Components has throughout the years developed and mastered five key technologies that address all four objectives.
…with five key technologies
At the heart of the new FBR53-HC design lies FCL Components' proven U-shaped twin contact solution. Using two contact points instead of one results in fewer ‘bounces’ during inrush load conditions, thanks to an evenly balanced load distribution. As a consequence, contact and thermal resistance are halved. This not only more than doubles its lifespan, but also makes the new relay far more reliable, preventing condensation and withstand freezing at low temperatures. Another design feature preventing failure due to condensation is the positioning of the twin contacts. These are situated at the top of the coil, increasing the distance to the PCB. The addition of knurling on the inside walls of the plastic cover, ensuring an extra tight fit, prevents the ingress of contaminants, even in harsh environments and operating conditions, hence boosting reliability over a much longer lifespan.
All these strict design features to keep the outside world out would not be much use if unwanted particles have already entered the tightly sealed relay during production. For this purpose, FCL Components has developed a unique manufacturing process that ensures high-quality end products. Measures to avoid contamination include blowing very clean, compressed air from all directions during each process step. These fully automated steps take place in clean room conditions to ensure the best quality.
FCL Components' new FBR53-HC is now ready to be soldered and sit modestly on a next-generation power management circuit board.